Metodologías de productividad de las operaciones
Metodologías de productividad de las operaciones
Mejorar la productividad de una planta de fabricación implica un planteamiento polifacético que aborde diversos aspectos del proceso de producción. He aquí una guía completa para desarrollar un proyecto destinado a mejorar la productividad:
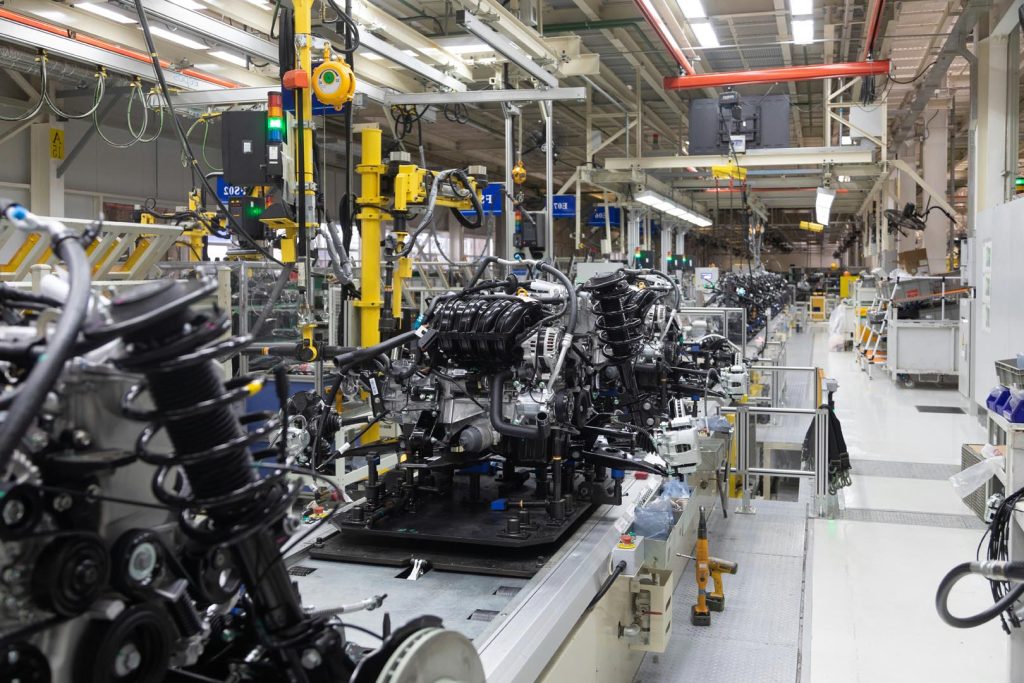
1. Planificación del proyecto y fijación de objetivos
- Definir objetivos
Aumente la producción sin incrementar los costes. Reduzca los tiempos de inactividad y los residuos. Mejorar la calidad y la uniformidad de los productos. Aumentar la eficiencia y la satisfacción de los empleados. - Establecer KPI (indicadores clave de rendimiento) Índice de producción (unidades/hora). Índice de utilización de la máquina. Porcentaje de tiempo de inactividad. Tasa de desechos. Eficacia de la mano de obra.
2. Análisis del estado actual
- Recogida de datos
Recopilar datos sobre los índices de producción actuales, el rendimiento de las máquinas y la productividad de los empleados. Utilice estudios de tiempo-movimiento para comprender el flujo de trabajo e identificar cuellos de botella. - Análisis DAFO
Identificar las fortalezas, debilidades, oportunidades y amenazas relacionadas con las operaciones actuales.
3. Identificar las áreas de mejora
- Cuellos de botella
Señale las áreas en las que se producen retrasos o ineficiencias con mayor frecuencia. - Tecnología
Evaluar el potencial de automatización y la implementación de tecnologías de fabricación avanzadas (por ejemplo, IoT, IA, robótica). - Procesos
Evaluar los procesos actuales en busca de ineficiencias y oportunidades para las técnicas de fabricación ajustada (por ejemplo, 5S, Kaizen, Six Sigma). - Plantilla
Examinar las competencias de los empleados y sus necesidades de formación.
Evaluar las estrategias de gestión y motivación laboral.

4. Desarrollar estrategias de mejora
Optimización de procesos
Aplicar los principios de fabricación ajustada para racionalizar los flujos de trabajo y reducir los residuos. Utilice el mapeo del flujo de valor para visualizar y mejorar el proceso de producción.Integración de la tecnología
Implantar el mantenimiento predictivo mediante sensores IoT para reducir los tiempos de inactividad imprevistos. Utilizar sistemas ERP (Enterprise Resource Planning) para una mejor gestión de los recursos.
Invierta en la automatización de tareas repetitivas.
Formación de los trabajadores
Ofrecer programas de formación para mejorar las cualificaciones de los empleados. Fomentar una cultura de mejora continua y participación de los empleados.Control de calidad
Aplicar medidas de control de calidad más estrictas para reducir los defectos. Utilice el control estadístico de procesos (CEP) para supervisar la calidad de la producción.
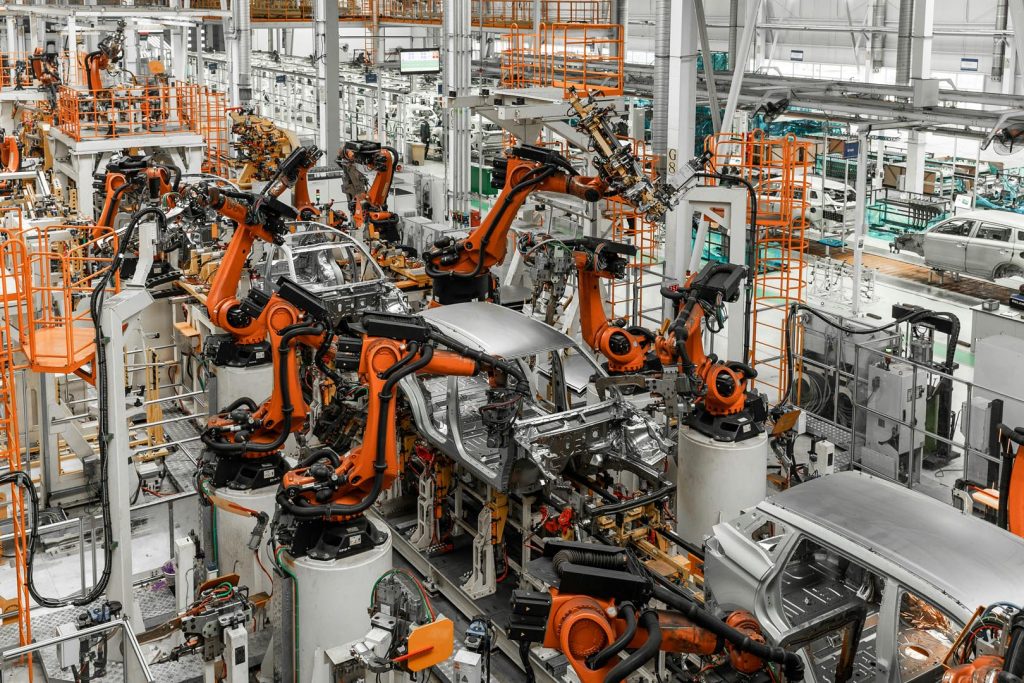
5. Plan de aplicación
- Proyectos piloto
Empezar con proyectos piloto a pequeña escala para probar nuevos procesos o tecnologías.
Recopile información y realice ajustes antes de la aplicación a gran escala. - Calendario e hitos
Elabore un calendario detallado con hitos y plazos concretos. - Asignación de recursos
Asignar recursos, incluidos presupuesto, personal y equipos, a las distintas partes del proyecto. - Gestión del cambio
Planifique la gestión del cambio para garantizar transiciones fluidas. Comunique eficazmente los cambios y beneficios a todas las partes interesadas.
6. Seguimiento y evaluación
- Control continuo
Utilice herramientas de supervisión en tiempo real para seguir los avances con respecto a los indicadores clave de rendimiento.
Celebrar reuniones periódicas para revisar los avances y abordar los problemas. - Bucle de retroalimentación
Cree un circuito de retroalimentación en el que los empleados puedan informar de los problemas y sugerir mejoras. - Ajustes
Prepárese para realizar los ajustes necesarios en función de las reacciones y los datos de seguimiento. - Informes
Informar periódicamente de los progresos a la dirección y a otras partes interesadas.
7. Mantener las mejoras
Normalización
Estandarizar los procesos y prácticas de éxito en toda la planta.Mejora continua
Fomentar una cultura de mejora continua en la que se anime a los empleados a sugerir y aplicar mejoras.Revisión y actualización
Revise periódicamente los resultados del proyecto y actualice las estrategias según sea necesario para adaptarse a las circunstancias cambiantes y a las nuevas tecnologías.
Con Business Interchalleng, puede mejorar sistemáticamente la productividad de una planta de fabricación, garantizando el éxito a largo plazo y la competitividad en el mercado.